3 Ways to keep a cleanroom ‘clean’ – surfaces, air, operation
We will try to explain what a cleanroom is and how to keep it clean. The three most important aspects of the cleanroom are:
- Surfaces
- Air
- Operation
What is a cleanroom?
A cleanroom is an environment, with a low level of environmental pollutants such as dust, airborne microbes, aerosol particles, and chemical vapors. It has a controlled level of contamination that is specified by the number of particles per cubic meter at a specified particle size.
How to keep a cleanroom “clean”
1. Surfaces
The surfaces and the equipment within the room:
- Should be smooth and impermeable
- Should not generate contamination i.e, create dust, or peel, flake, corrode or provide a habitat for bugs
- Are easy to clean. i.e., all surfaces are easily accessible and are easily decontaminated

2. The control of air through the cleanroom
- The amount of air introduced and removed from a cleanroom is tightly controlled
- Cleanrooms are generally pressurized, which is achieved by taking out slightly less air than is put in
- Air is kept moving throughout the room
- The air taken out of the room is usually recirculated through the air handling system where filters remove the contamination. The air is then recycled back into the room

3. The way the cleanroom is operated
The most effective way of maintaining the air quality in a cleanroom is to operate it properly. This involves:
- Strictly controlling access to trained personnel – people are the largest source of contamination
- Regularly cleaning to strictly controlled procedures
- Regular maintenance of equipment

Electronic Application: A market leading provider of award-winning bond test and x-ray inspection systems for electronic components
Why Speedor Cleanroom?
- The fabric of the Speedor Cleanroom is multilayer PVC and textile, which combine to ensure strength, tear resistance and long life.
- Top roll and motor covers minimise particle accumulation.
- Optional stainless steel components for maximum cleanliness.
- The non-touch safety light curtain maintains the clean lines of the door system and reduces hygiene risks to an absolute minimum.
- Smooth finishing surface for ease of cleaning
- Sloping edges reduce the collection of dirt and reduce pooling of cleaning fluids
- Air Permeability – Depending on opening size and pressure differentials over the doorway, for example, our test door achieved the following

- The side frame design ensures the closest tolerances possible to maintain pressure seals
25mm neoprene draught blade seal, creating a continuous seal from the curtain to the floor ensuring the lowest possible pressure loss - Each door is designed with the capability of adjusting the air leakage rates using the integrated adjustable ventilation system

The Speedor Cleanroom is designed for frequent use in cleanroom applications and is suitable for areas requiring Isoclass 6-8 such as:
- Pharmaceutical production
- Food manufacturing
- Medical/Biotechnology production
- Electronics/Semiconductor production
- Aerospace/Automotive production
- Chemical/Environmental Analysis

Speak to us about how we can help you solve logistical challenges with a completely tailored high-speed door solution.
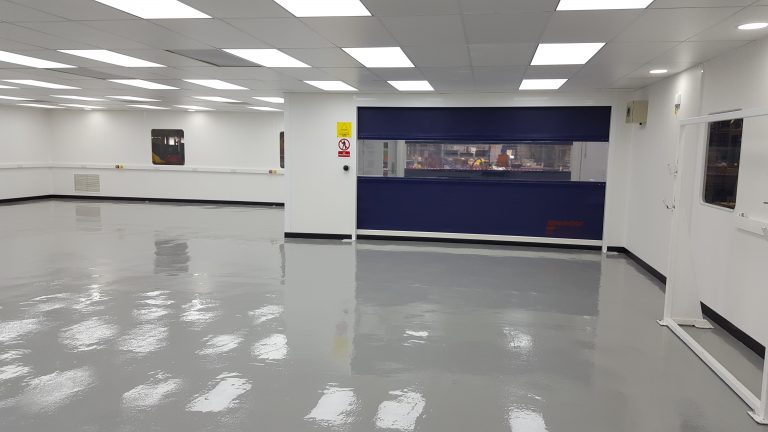